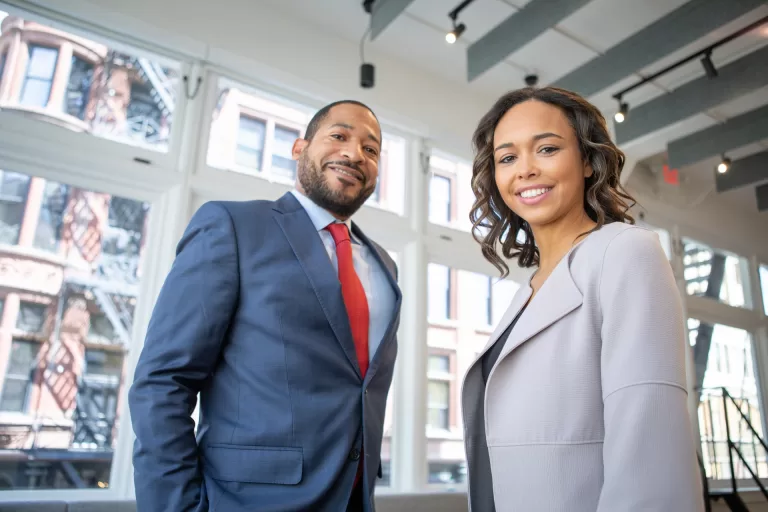
Business Process Management and corporate governance
Business Process Management and corporate governance Linkedin Youtube Facebook Instagram A company is a group of people with a common
Health institutions must have the highest quality standards because of the importance of their activity. Health being the base of human life, processes must be of the best quality there, as long as the activities in those institutions decide on a person’s life or death. In times of crises and extreme demands, as the current pandemics, these organizations have seen the importance of having the aid of certain technological solutions that allow them to fasten their processes through automation. Besides, automation and quality control are a perfect complement.
During the last years a new vision of performance, personal and corporate, has gain popularity: the idea of producing different changes in the environment in order to improve the behavior of a given individual. One of the premises of these strategies for improvement is that what is not measured cannot be improved:
Imagine this: Someone walks into the gym, warms up, does a little bit of this exercise, does a little bit of that exercise, bounces around to a few machines, maybe hops on the treadmill, finishes their workout, and leaves the gym. This isn’t a critique of their workout. In fact, it’s quite possible that they actually got in a nice workout. So, what is notable about this situation? They didn’t measure anything. They didn’t track their workout. They didn’t count reps or weight or time or speed or any other metric. And so, they have no basis for knowing if they are making progress or not. Not tracking your progress is one of the six major mistakes I see people make in the gym (lifehack.org).
The reason is clear: if we are not aware of how much we have done of some exercise, we won’t be able to know if in a week from now we will have improved our resistance or if we have gone backward, if we are running faster or longer, or if we are actually losing strength. Only by knowing these variables we can stablish how is going our progress and from there we can set clear improvement goals.
Now, on the same example, we can think that for having a recording we have to use our memory. In order to record all the exercises, the numbers, the used machines, the repetitions, we should need a very potent memory, or have a pad and a pen with us for each annotation. This becomes quite cumbersome and is a waste of time and attention, attention that could be focused on exercise itself. But, if we have a device for automatically registering the pulse, the number of steps, the miles made, burnt calories, repetitions, etc., we won’t have to worry for writing anything and we know that recordings will be digitally stored so we can go on them on the appropriate moment.
Thus, automation and quality control are part of the very same strategy: if we automate processes through informatic technologies, we guarantee an automatic recording of everting that is happening during the operation and we can later check all this information to see if everything is working according to the plan.
Business Process Management solutions seek for the automation of a great deal of processes in organizations. In this way the operation is fastened and optimized because we eliminate different kinds of issues:
That can mean optimizing resource allocation, eliminating bottlenecks, reducing process duplication, speeding up transactions, etc. Employing this outcome-oriented methodology helps organizations deliberately improve operations, as well as their bottom line. In doing so, they can become stronger and more prepared to weather any storms influenced by the market (outsystems.com).
Thus, by implementing this solution we can improve the operation as it is known. However, in addition of the improvement of what we already have, automation allows that constant recording of information for us to be able to check on it later and improve new aspects or something that we haven´t noticed yet. This means that from that information we can generate new plans for action, formulate new strategies for marketing, develop new products, stablish new channels for customer attention, etc., and form this the general impact of the company can be improved.
All this means a corporate growth that wasn’t possible without the measures allowed by BPM. For that reason, automation and quality control are actually two inseparable aspects, for the amount of information circulating in business is so big that we can no longer trust just in human memory, manual abilities, intuition, etc.
This is the vision that has guided Dexon BPM development. We have posed as a goal the development of a tool that can be useful not only for automation, but a help for achieving a continual improvement due to the connection there is between automation and quality control. We have thus seen that our customers improve significantly and can bring to their clients more rapid answers and innovation proposal for customer attention. In these times of changes, furthermore, we see the urgent necessity for the use of technology for business optimization.
Business Process Management and corporate governance Linkedin Youtube Facebook Instagram A company is a group of people with a common
Linkedin Youtube Facebook Instagram The BPM methodology seeks to use information technology to automate as many activities in an organization
How BPM aligns with the organization’s strategy Linkedin Youtube Facebook Instagram An organization is a group of people, resources, techniques,
Artificial intelligence for business optimization Linkedin Youtube Facebook Instagram Perhaps the technological trend that is currently the strongest and the
How to consolidate remote work in your business Linkedin Youtube Facebook Instagram Many organizations had to assume remote work as
The future of remote work Linkedin Youtube Facebook Instagram Working from home, working from the train, in the car, working